Automotive
The Prestige Automotive Recruitment Team specializes in original equipment and after-market manufacturers/suppliers. In addition, the Automotive Recruitment Team serves OEM component manufacturers in the aerospace, construction, heavy truck, off-highway, appliance and industrial markets. Typical assignments include a full range of “customer focused” positions (Sales / Sales Management, Account Management, Applications, Program Management, Marketing), Technical Disciplines (most engineering specialties, manufacturing, research &development, quality /process control) and a full-range of accompanying management assignments from middle management to senior executive positions.The Automotive Recruitment division has completed numerous assignments for a full range and size of client firms…from multi-national, Fortune 500 companies to mid-level public and privately held manufacturers as well as smaller “up and coming” organizations. While the epicenter for automotive is Detroit, our team has completed assignments for U.S. and Off-Shore clients throughout North and South America, Latin America, Asia and Europe. Let Prestige be your first and only choice when looking for exceptional Candidates who will take your business to the next level.
The Automotive Industry in the United States began in the 1890s and, as a result of the size of the domestic market and the use of mass-production, rapidly evolved into the largest in the world. However, the United States was overtaken as the largest automobile producer by Japan in the 1980s, and subsequently by China in 2008. The U.S. is currently second among the largest manufacturer in the world by volume, with approximately 8-10 million manufactured annually. Notable exceptions were 5.7 million automobiles manufactured in 2009 (due to crisis), and peak production levels of 13-15 million units during the 1970s and early 2000s.
The motor vehicle industry began with hundreds of manufacturers, but by the end of the 1920s it was dominated by three large companies: General Motors, Ford, and Chrysler. After the Great Depression and World War II, these companies continued to prosper, and the U.S. produced nearly three quarters of all automobiles in the world by 1950 (8,005,859 of 10,577,426). Beginning in the 1970s, a combination of high oil prices and increased competition from foreign auto manufacturers severely affected the companies. In the ensuing years, the companies periodically bounced back, but by 2008 the industry was in turmoil due to the aforementioned crisis. As a result, General Motors and Chrysler filed for bankruptcy reorganization and were bailed out with loans and investments from the federal government. But according to Autodata Corp, June 2014 seasonally adjusted annualized sales is the biggest in history with 16.98 million vehicles and toppled previous record in July 2006.
Prior to the 1980s, most manufacturing facilities were owned by the Big Three (GM, Ford, Chrysler) and AMC. Their U.S. market share has dropped steadily as numerous foreign-owned car companies have built factories in the U.S.
Toyota had 31,000 direct employees in the U.S. in 2012, meaning a total payroll of about $2.1 billion, compared to Ford’s 80,000 U.S. employees supplying their 3,300 dealerships and Chrysler’s 71,100 U.S. employees supplying their 2,328 dealerships.
Development History
Development of Automobile Components
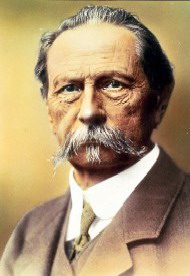
After the invention of the automobile by Karl Benz in 1886, various changes were made to self-powered vehicles so they were better suited to human abilities, changed based on experience with animal-drawn vehicles. Actually, the meaning of making vehicles, which is based on self-power, is that they need many kinds of part such as brakes, handles and gauges. Interestingly, for example, the origin of seat belts purpose was to keep passengers in their seat, not to keep them safe in the case of accident.
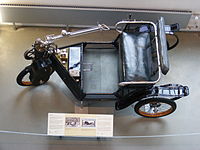
The improvement of automobile parts was inevitable because the people needed to get abilities to control their self-powered vehicle. First of all, the steering mechanism is indispensable factor.The steering wheel in very early automobiles was a tiller, a lever arm that connected to the pivot point of the front wheels, a design derived from small boats. Tillers were easy to use for very slow speeds and lightweight vehicles (such as those with three wheels). However, steering a jolting tiller with sheer muscle power was difficult for heavy four-wheel vehicles moving at high speed. After tiller, a bar handle with grips at both ends to be held with both hands was introduced that could be held more firmly than the tiller. A round steering wheel, able to be turned by muscle power and easier to hold in the hands, was first introduced around 1895.
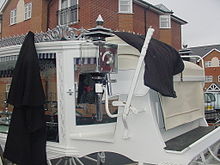
The brake system for very early self-powered vehicles consisted of a wooden block pressed against one of the wheels using a hand-operated lever, a technology adapted from horse carriages. A foot pedal to operate the band brake first appeared in Benz Velo in 1894. The foot-operated pedal could exert greater force than a hand brake and allowed a driver to use both hands to hold a steering wheel. This could be why the steering wheel and the foot pedal appeared in the same period.
Early automobiles were not equipped with any gauges. Oil-pump gauges were the first instruments installed inside vehicles, allowing drivers to confirm the oil flow and to inject additional oil when necessary. Water-pressure gauges were also introduced around 1900. Durability was the biggest issue in the early stage of automobiles. Therefore, general monitoring of the condition of unreliable vehicles by the driver was critical and consumed considerable attention. The speedometer was introduced after 1900. It was mounted outside of the bulkhead separating the engine and cab, where its cable easily fits. The speedometer was introduced to highlight the vehicle’s high-speed capability. In the USA, the state of Connecticut imposed a speed limit of 8 mph within the city and 12 mph outside of the city in 1901, thus encouraging speedometer installation.
In summary, the first human factors development was designing controls for the primary driving task, such as the steering wheel and the brake pedal, which allowed for operation of a heavy self-powered vehicle using only muscle power. The second development was introducing gauges to inform the driver about the mechanical condition of the vehicle and then driving condition (speedometer).[10][11]
Development of the Work Life
The type of life in the job, which the Automobile industry workers went through, developed rapidly between 1900 and 1930s. This development accompanied the shift caused by the progress of mass production; including using different methods to improve the efficiency of the assembly line, and the advancement of the machines used to assemble the cars as wells as the ones used to make the auto parts. As a result, the life in the job kept changing, leaving the workers entirely unsatisfied.
In the early years, manufacturing automobiles involved putting together parts that have been already built by some other shop. Also, manufactures were made of many groups stretched around the factory with each group made of 2 to 3 men working together to build a whole car. However, most of the factories, which use this procedure, did not have any kind of methodology at the early years.
The car assembling began to reach some kind of organized system around 1912. At the same time, factories started making the elements used to assemble an automobile themselves rather than having an arrangement with an outside shop. The manufacturers build the parts employing the same techniques they developed to produce the final product.
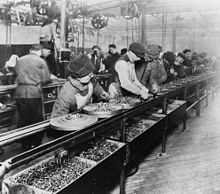
The factories began improving mass production by arraying the automobile’s structuring line in a way that allow the employees to either go from one car to another, or having the automobile cruised to their station by a small trailer. However, manufacturers such as Oldsmobile started applying similar type of moving production as early as 1901. During this process the working force for the automobile industry became more dependent on the idea of being efficient rather than being gifted.
By 1913 it became viable to introduce steadily moving assembly line. In the summer of that year, Ford had already begun testing different routines to progress the assembly line in order to attain the most productive method to produce an automobile. Before introducing the moving assembly line, the mean time it took to produce one car frame was around twelve and a half hours. By the time those moving assembly were finished, Ford became able to decrease the time needed to create each chassis to only one hour and thirty-three minutes, allowing them to produce an average of 1200 cars in a single day.
In 1910, Almost 75% of the workforce in the automobile industry was categorized as experienced jobs. Around the middle of 1920s, less than 10% of the industry’s employees were considered skillful.
Development of Production
For decades, through times economic plenty and recession during the 20th century, the American automotive industry has had a tremendous impact on the US economy. The number of new cars produced annually was a reliable indicator of the nation’s economic health. As a result of economic prosperity in the United States, the growth of the automobile industry began to expand from just the wealthy to become more accessible to other members of society. As the automotive market began to expand it became evident that volume lay in low-priced, light cars, to which Henry Ford rightly responded with the Model T in 1908. Like Ford’s Model T, innovators quickly adapted to the needs of the consumers to produce at a level of output that would keep up with rising demand.
During the early 1900s, companies rushed to implement large-volume output technology, including a rapid changeover to a new manufacturing process designed to produce massive quantities of identical high-quality goods at a low cost per unit. As such, the stages of assembly were standardized, utilizing precision-made, interchangeable parts and factories carefully reorganized to allow the flow of raw materials through a set of sequential steps. This was a remarkably new technology that changed the landscape for manufacturing goods. Now, by making productions standardized and by creating interchangeable parts mass production was made possible. These innovations caused a great advancement in the American automobile industry that continued for decades.
Soon, new manufacturing methods dramatically altered the organization of the workplace, modifying the concept of the American factory environment at the time. The assembly line was instituted, creating a production plan that required a minute division of labor, which meant that each person performed a single tedious task. By so doing, production increased and became more efficient requiring no additional labor costs.
By 1916 cars began selling at $875, which by today’s standards would be around $18,500. Soon, the market widened with the mechanical betterment of the cars, the reduction in prices, and the introduction of installment sales and payment plans. Yet during the period from 1917 to 1926 the annual rate of increase in sales was considerably less than from 1903 to 1916. In the years 1918, 1919, 1921 and 1924 there have been absolute declines in automotive production. The automotive industry caused a massive shift in the industrial revolution because it accelerated growth by a rate never before seen in the US economy. The combined efforts of innovation and industrialization allowed the automotive industry to take off during this period and it proved to be the backbone of United States manufacturing during the 20th century.
From Wikipedia, the free encyclopedia